Safety Inspection-Lockout and Tagout
This mobile app is used to track safety procedures related to ensuring that industrial machinery is properly shut off and not restarted until maintenance or servicing work has been completed.
5,000 Companies save time and money with GoCanvas
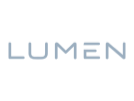
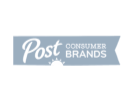
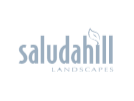
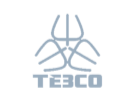
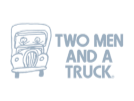
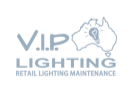
Lockout and tagout procedures (also known as loto procedures), require energy isolation for hazardous power sources before equipment and machinery repairs are started. Using the loto procedures app helps ensure that workers have a clear process for dealing with dangerous machinery and simplifies loto procedures according to OSHA standards, and the health and safety requirements of the job site.
A critical element to any occupational safety and health process, the lock and tag app is an important tool designed to protect the health and safety of those who work around industrial machinery and equipment. Instead of relying on paper checklists for OSHA lockout inspections, this easy to use app makes it easy to stay on track with your construction site's loto program. This app helps you make sure workers have a clear process for dealing with dangerous machinery and is a helpful tool in improving occupational safety and health. Easily accessible from any smartphone or tablet, the app comes with date, time and signature capture, and can be easily customized to meet your company's needs.
Use this lockout tagout periodic inspection form to meet occupational safety goals related to industrial machinery energy sources as part of an improved energy control program. Create an occupational safety and health standard for employee training and work operations related to machinery and equipment. Ensure that hazards are identified in advance as part of a sound lockout tagout policy in the workplace.
GoCanvas accounts come
with hundreds of form templates
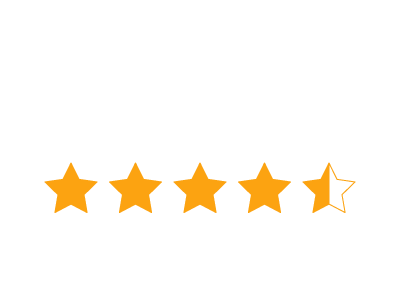
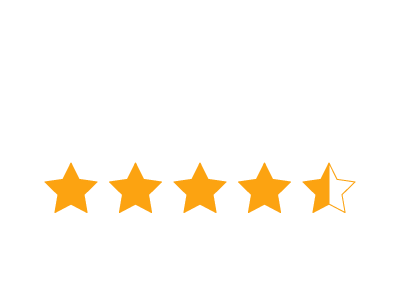
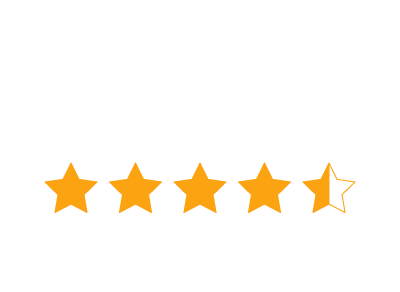
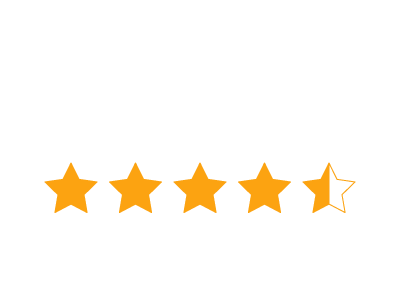
Don't take our word for it...
“I’m not a tech guy and I was able to pick this thing up in probably an hour, and actually start to build apps. I’ve done them over lunch when I’ve gotten frustrated with a process that didn’t exist in our company. So for non tech people who’ve got a problem, the support here is awesome and I’d recommend it to anybody, not just in our industry.”